Valve Jobs

In the intricate world of industrial machinery, the role of valves is often understated yet incredibly crucial. Valves are the unsung heroes that regulate the flow of various substances, from gases and liquids to solids in granular form, in countless industries worldwide. This article delves into the diverse types of valve jobs, their specific functions, and their significance in maintaining the efficiency and safety of industrial processes.
The Diverse Landscape of Valve Jobs

Valves are not a one-size-fits-all component; they come in various shapes, sizes, and mechanisms, each designed for specific applications. Understanding the different types of valve jobs is essential for professionals in the industrial sector, as it directly impacts the selection, maintenance, and optimization of these vital components.
1. Gate Valves: The On/Off Masters
Gate valves are the workhorses of the valve world. They are primarily used for isolating or stopping flow in a pipeline. The unique design of gate valves, with a wedge-shaped gate that rises and lowers to control flow, makes them ideal for applications requiring full flow or complete shut-off without causing excessive pressure drop. This type of valve is commonly found in water treatment plants, oil refineries, and chemical processing facilities.
In the context of a real-world application, imagine a large-scale manufacturing plant that requires a complete shutdown for maintenance. Gate valves would be strategically placed to control the flow of various substances, ensuring a safe and efficient shutdown process.
Gate Valve Advantage | Real-World Benefit |
---|---|
Low Pressure Drop | Minimizes energy consumption and equipment wear. |
Full Bore Opening | Allows for unobstructed flow, reducing the risk of blockages. |

2. Globe Valves: Precision Control Experts
Globe valves are designed for precise control of flow rate. Unlike gate valves, which are primarily for on/off applications, globe valves excel at regulating flow. The distinctive design, with a disc that moves up and down to control flow, allows for fine adjustments. This type of valve is commonly used in heating and cooling systems, as well as in chemical plants where the control of flow is essential for process optimization.
Consider a pharmaceutical manufacturing plant where the precise control of temperature is crucial for drug production. Globe valves would be integral to this process, ensuring the right flow rates and temperatures are maintained at every stage.
Globe Valve Feature | Benefit in Practice |
---|---|
High Control Accuracy | Enables precise adjustments, ensuring optimal process conditions. |
Wide Range of Sizes | Suited for various applications, from small labs to large-scale production. |
3. Ball Valves: The Quick-Acting Solution
Ball valves are renowned for their quick and reliable operation. With a simple quarter-turn, the ball with a hole in it rotates to either allow or block flow. This type of valve is commonly used in natural gas distribution systems, where rapid shut-off is critical for safety. Ball valves are also found in water distribution systems and chemical plants, where their durability and ease of operation are highly valued.
Think of a natural gas pipeline network. Ball valves would be strategically placed to ensure quick shut-offs in the event of a leak or emergency, minimizing the risk to the public and the environment.
Ball Valve Advantage | Real-World Impact |
---|---|
Rapid Operation | Enables quick response to emergencies, enhancing safety. |
Low Maintenance | Reduces operational costs and downtime. |
4. Butterfly Valves: The Compact Regulators
Butterfly valves are known for their compact design and ease of installation. With a disc that rotates to control flow, they are often used in applications where space is limited. Despite their compact size, butterfly valves can handle high-pressure and high-temperature applications, making them versatile in the industrial world. They are commonly found in water treatment plants, wastewater treatment facilities, and in the food and beverage industry.
In a water treatment plant, butterfly valves might be used to control the flow of water during various treatment stages, ensuring efficient and controlled processing.
Butterfly Valve Feature | Practical Application |
---|---|
Compact Design | Ideal for space-constrained environments, such as narrow pipelines. |
Wide Size Range | Suited for various flow rates, from small to large. |
5. Check Valves: The Backflow Preventers
Check valves, also known as non-return valves, are designed to prevent the backflow of fluids. They allow flow in only one direction, ensuring the system remains protected from potential contaminants or reverse flow issues. Check valves are commonly used in sewage systems, where they prevent the backflow of sewage, and in water distribution systems to maintain pressure and prevent contamination.
Imagine a sewage treatment plant. Check valves would be crucial to ensure that treated water flows in the right direction, preventing any backflow of untreated sewage.
Check Valve Function | Real-World Application |
---|---|
Backflow Prevention | Ensures system integrity and prevents contamination. |
Wide Variety | Available in different designs to suit various applications and pressure requirements. |
Valve Performance and Maintenance

The performance and longevity of valves are critical factors in industrial operations. Regular maintenance and the use of high-quality components are essential to ensure optimal performance and avoid costly downtime. Here are some key considerations for maintaining valve performance:
- Regular Inspection: Conduct routine inspections to identify any signs of wear, corrosion, or damage. This can help prevent major issues and ensure timely repairs or replacements.
- Proper Lubrication: Ensure that valves are adequately lubricated, especially in high-pressure or high-temperature applications. This can prolong the life of the valve and maintain its smooth operation.
- Valve Sizing: Selecting the right size valve for the application is crucial. An undersized valve can lead to pressure drops and inefficiencies, while an oversized valve may not provide the necessary control.
- Material Selection: The choice of material for a valve depends on the application. For instance, stainless steel valves are often used in food and beverage industries due to their corrosion resistance and ease of cleaning.
Real-World Maintenance Case Study
Consider a power generation plant that relies on steam turbines. The plant’s gate valves, which control the flow of steam to the turbines, require regular maintenance. Technicians inspect the valves for any signs of wear or corrosion, ensuring that the seats and seals are in good condition. Proper lubrication is applied to maintain the smooth operation of the valves, which are critical for the efficient functioning of the steam turbines.
The Future of Valve Technology
The valve industry is continuously evolving, with new technologies and innovations shaping the future of valve design and performance. Here are some trends and developments to watch for:
- Smart Valves: The integration of smart technologies into valves is a growing trend. These valves can monitor their own performance, providing real-time data on flow rates, pressure, and potential issues. This data can be used for predictive maintenance, optimizing performance, and reducing downtime.
- 3D Printing: 3D printing technology is being explored for valve manufacturing, offering the potential for customized, on-demand valve production. This could revolutionize valve replacement and customization, particularly in unique or emergency situations.
- Corrosion-Resistant Materials: Advances in materials science are leading to the development of new, highly corrosion-resistant materials for valve construction. This can significantly extend the lifespan of valves in corrosive environments, such as chemical processing plants.
- Valve Automation: The automation of valve operations is becoming increasingly common, especially in industries where precise control and remote operation are advantageous. Automated valves can be controlled remotely, offering enhanced safety and efficiency.
Conclusion
Valves are the silent guardians of industrial processes, ensuring the safe and efficient flow of substances. Understanding the diverse range of valve jobs and their specific functions is crucial for professionals in the industrial sector. From gate valves for complete shut-offs to globe valves for precise control, each type of valve has a unique role to play. Regular maintenance, proper sizing, and material selection are key to ensuring valve performance and longevity. As the valve industry continues to innovate, the future looks bright with advancements in smart technologies, materials, and automation enhancing the capabilities and reliability of these essential components.
Frequently Asked Questions
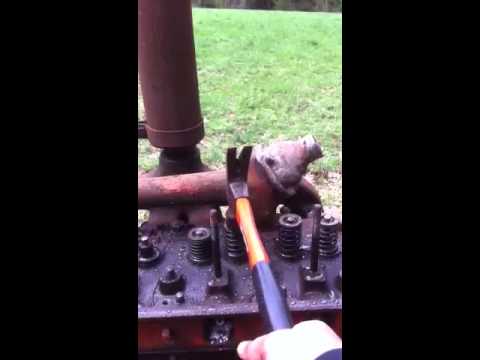
What are the key factors to consider when selecting a valve for a specific application?
+
When choosing a valve, key factors include the type of fluid being controlled (liquid, gas, or solid), the required flow rate, pressure and temperature conditions, and the desired level of control (on/off or modulating). Other considerations include the valve’s material compatibility with the fluid, its size and installation constraints, and the level of maintenance and reliability required.
How often should valves be inspected and maintained?
+
The frequency of valve inspection and maintenance depends on the valve’s application and environment. In critical or high-pressure/temperature applications, more frequent inspections are necessary. As a general guideline, valves should be inspected at least annually, with more thorough maintenance and repairs performed based on the inspection findings and the valve’s condition.
What are some common issues that can affect valve performance and how can they be addressed?
+
Common issues with valves include wear and tear, corrosion, leaks, and obstructions. Regular maintenance and timely repairs can address these issues. In the case of wear and tear, replacing worn parts like seats and seals can restore valve performance. For corrosion, using corrosion-resistant materials or coatings can help. Leaks can be addressed by tightening connections or replacing gaskets, while obstructions may require cleaning or the replacement of valve components.
How can smart valve technology improve industrial processes?
+
Smart valve technology integrates sensors and data analytics into valves, allowing for real-time monitoring of valve performance and conditions. This data can be used for predictive maintenance, optimizing valve performance, and reducing unplanned downtime. By providing valuable insights into the health of the valve and the process it’s controlling, smart valves can enhance operational efficiency and safety in industrial processes.
What are the benefits of valve automation in industrial applications?
+
Valve automation offers several benefits, including increased operational efficiency, reduced labor costs, and enhanced safety. Automated valves can be controlled remotely, allowing for precise and timely adjustments to flow rates and pressures. This is especially advantageous in hazardous environments or situations where quick responses are critical. Additionally, valve automation can reduce human error and improve overall process control.